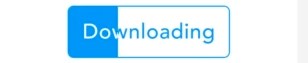

You can use couplers to more easily define complex relative motion between two components. New Assembly Constraints A coupler is a type of constraint that defines the relative motion of two joints.With embedded GD&T (PMI, FTA) tolerancing your model and Joints and Constraints brought in as 3DCS Moves, a user only has to create Measurements to complete their Tolerance Analysis Model. Extracting Joints and Constraints from CAD can make model creation easy.Created a contact interaction (friction coefficient of 0.12) 5. Created a kinematic constraint on a reference point (in the center of the gear) to its inner surface, in order to emulate the shaft 4. Created the material, section, and assigned section to parts 3. Created and imported a Solidworks file for the gears 2.

#Simply fortran keygen crack how to
Tutorial 1 – SolidWorks User Interface Tutorial 2 – Introduction to SolidWorks Tutorial 3 – How to create simple box Tutorial 4 – How to create simple plate Tutorial 5 – How to create allen key Tutorial 6 – How to create 17" wheel Tutorial 7 – How to sheet metal part Tutorial 8 – How to create spring Tutorial 9 – How to.The gear ratio in the motion constraint is set to 0.5 so I'm confused as to why the two gears are shown to be spinning at the same rate. I have attached a screenshot of the resulting velocities and what my assembly looks like. After running the simulation, I have played around in the output grapher but I can't make sense of the data.HDRI Lighting a model, precise conversion, 4 way symmetry, precise measurement, sketch constraints, Power Shelling, and all the new updates in the latest 6.1 release Power Surfacing and Power Surfacing RE for SolidWorks.Using various results from inspire a gear was Topology optimization on the gear was performed using Altair INSPIRE V9.5 and the CAD model of the gears was created using SOLIDWORKS 2016 and the optimized gear was analyzed in ANSYS 16.0. method is used for ideal material distribution of gear structure such that the objective function is maximized.Because the Simscape™ Multibody™ Link exporter does not support this constraint, exporting this assembly results in an XML file in which the gear constraint is replaced by a rigid connection between. The two gear parts are constrained by a Gear mate in the SolidWorks® assembly. In this assembly, two gear parts mesh with a gear ratio of 2:1.Every lesson and exercise in this book was created based on real world projects. It provides readers with a strong understanding of SolidWorks and covers the creation of parts, assemblies and drawings.

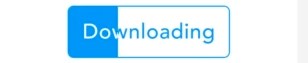